
However, surface defects are inevitable, initiated by degradation, temperature differences, fatigue loading, and foreign objects between the wheel and rail during train operation, then propagated through repeated extrusion caused by the contact stress between the wheel and the rail. Therefore, the steel rail is required to be clean and free of surface defects. Its performance directly affects the safety of railway transportation. In the high-speed railway system, the rail plays a dual role of carrying and guiding the running of the train. On the collected dataset with 8 defect classes, our algorithm achieves 7.4% higher mAP.5 compared with YOLOv5 and 2.8% higher mAP.5 compared with Faster R-CNN. Experimental results substantiate that the approach outperforms single detecting architecture in our specified rail defect task. A shared feature pyramid network is adopted to reduce model parameters as well as computation cost. Image augmentation and feature augmentation operations are randomly applied to further make the model more diverse. We apply multiple backbone networks individually to obtain features, and mix them in a binary format to obtain better and more diverse sub-networks. To overcome this challenge, motivated by ensemble learning that uses multiple learning algorithms to obtain better predictive performance, we develop an ensemble framework for industrialized rail defect detection. Selecting an appropriate model and tuning it with insufficient annotated rail defect images is time-consuming and tedious.
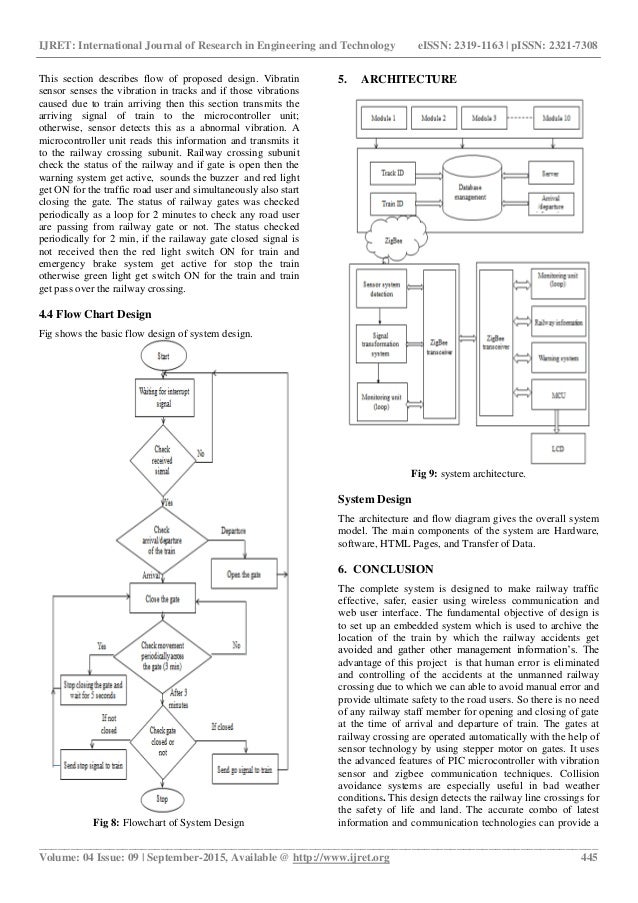
However, the CNN-based detection models are diverse from each other in performance, and most of them require sufficient training samples to achieve high detection performance.
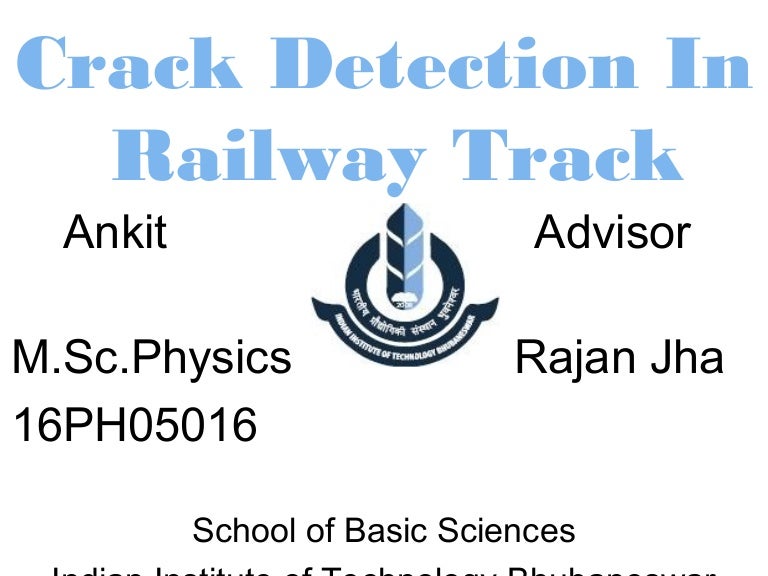

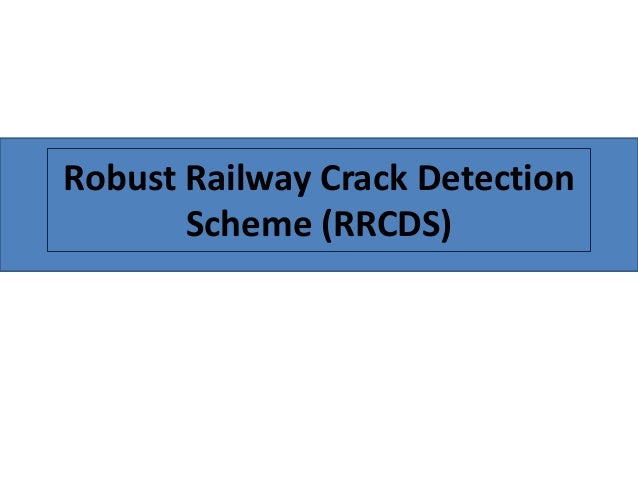
The CNN-based computer vision approach has been proved to be a strong detection tool widely used in various industrial scenarios. The detection of rail surface defects is vital for high-speed rail maintenance and management.
